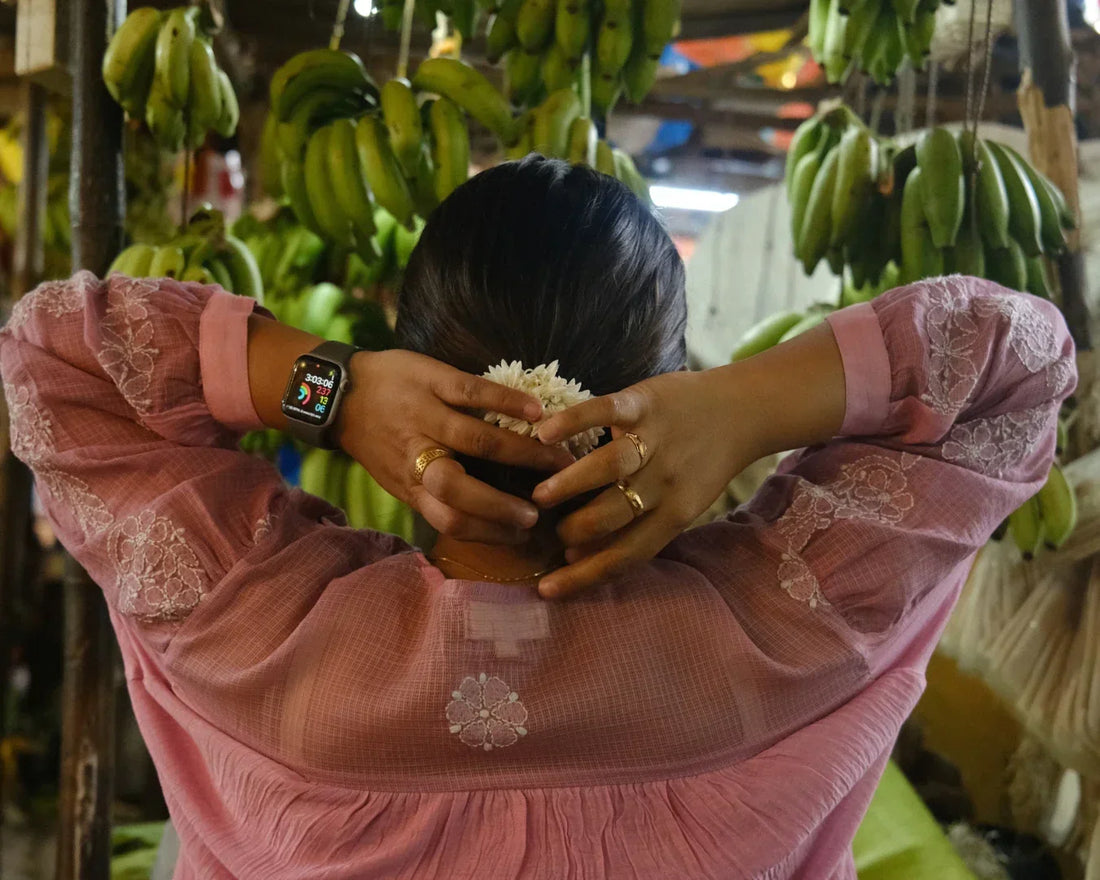
Types of Chikankari embroidery: White on White | Stitches and Shadows
Amhara StoriesSix basic stitches form the foundation of the embroidery, with combinations of these used to create intricate floral and leaf patterns. Some stitches start from the front of the fabric, others from the back.
Variants of the 6 main stitches
Rahet: A stemmed stitch that is hardly used in its basic form but is frequently utilised in the double version of Dora bakhiya.
Banarasi: A knotted stitch made on the right-hand side of the cloth using six threads. Banarasi Chikankari Sarees are very famous for the same.
Keel Kangan: This material is used to embellish floral designs and butties. This structure involves a ‘turra’ which is a round stud in the centre having tiny stitches around it.
Hool/Hole: a little detachable eyelet stitch. It is made with six strands and resembles the heart of a flower.
Zanzeera: after one or more outlines have been done, the Zanzeera stitch is used to delineate the leaf/petal forms finally.
Pechni: a line stitch in Chikankari and is widely used to outline shapes or mostly form stems to connect leaves, flowers and phandas.
Balda: a premium replacement of Pechni at places. Very tightly packed stitch.
Hathkati: a single line of jaali made by pulling apart the warp and the weft of the fabric by needle and thread. It will usually be seen in between a kauri or two pechnis or two pattis with a suitable space to craft it.
Kauri: a bud or shell kind of structures, which looks like two slim pattis are joined from both sides leaving in between space for hathkati.
Keherki: a premium stitch used in place of a keel or kangan. It is circular in shape having a hole in the centre.
Kante: tiny closely packed stitches outlining another stitch. Outlines of kante in a patti, bijli or other stitches immediately tell us that the piece is premium as it outlines a stitch which is itself crafted from before.
Fabrics used for Chikankari
Chikankari embroidery, renowned for its delicate beauty, can be crafted on a variety of fabrics. While traditionally done on a white muslin or mul base, also known as ‘Tanzeb’, modern Chikankari work incorporates both colored fabrics and threads, enhancing its appeal across diverse styles.
Silk(resham) and cotton threads are predominantly used for embellishing sarees, dupattas, table linens and kurtas. Though cotton remains the most common fabric, the embroidery is also executed on mul/mulmul, muslin, organza, chiffon, georgette, viscose, polyester, cotton crepe, linen and net.
The traditional process of creating Lucknawi Chikankari garments
The creation of Lucknawi chikankari garments is a meticulous process that blends artistry with precision.
- Fabric cutting and styling: The process begins with fabric cutting and styling, where the material is cut into the desired shape and stitched using a running stitch to form a semi-finished garment.
- Block-printing: Next comes ‘Chhapayi’, a traditional block-printing technique. Wooden blocks carved with floral, geometric, or border patterns are dipped in a dye mixture of glue and indigo, and pressed onto the fabric, creating temporary imprints to guide the embroidery.
- Embroidery: Once the block-printed fabric is ready, artisans begin the embroidery by hand, using fine needles and threads. Various Chikan stitches—such as Bakhiya (shadow work), Phanda (knot work), Keel Kangan (petal work), and Pechni (twisted stitches)—are employed to create intricate motifs, floral designs, and delicate butis.
- Washing and dyeing: After the embroidery is complete, the fabric is soaked and thoroughly washed to remove the block-printed dye.
- Starching and ironing: The final step involves starching and pressing the garment to achieve its characteristic stiffness and refined finish.
This labor-intensive method, passed down through generations, preserves the authenticity of Lucknawi Chikankari. Despite changes in fabric and style, the traditional craftsmanship remains central to its timeless appeal, making every piece a testament to the skill and heritage of the artisans.